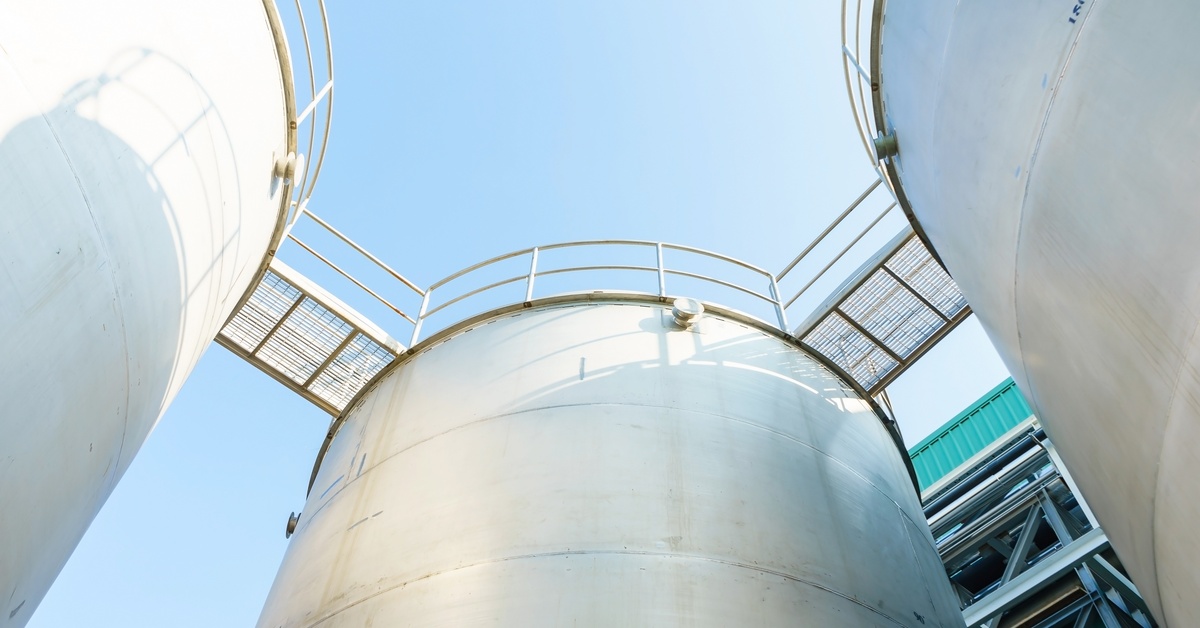
Advancements in technology are reshaping the industrial sector, and tank linings are no exception. Innovations in materials and application techniques have revolutionized the durability, performance, and longevity of industrial tank linings. These advancements are helping industries address challenges such as corrosion, chemical compatibility, and regulatory compliance with greater efficiency. There is a world of emerging technologies in industrial tank linings, and when you understand what the future looks like, you can better leverage linings in your own industry.
Epoxy-Based Coatings
Epoxy coatings have advanced significantly in recent years, offering enhanced chemical resistance and versatility. These durable linings are ideal for harsh industrial environments where protection from chemicals and abrasives is necessary. The latest formulations improve adhesion properties, ensuring better performance even in conditions involving high humidity or extreme pH levels.
Polyurethane Linings
Technological improvements in polyurethane linings have led to increased flexibility and impact resistance. They are particularly effective in applications requiring protection from physical wear and tear, such as tanks used in abrasive materials handling or processing industries. Polyurethane’s ability to resist cracking and deformation under pressure enhances its longevity and makes it a cost-effective choice for many industrial uses.
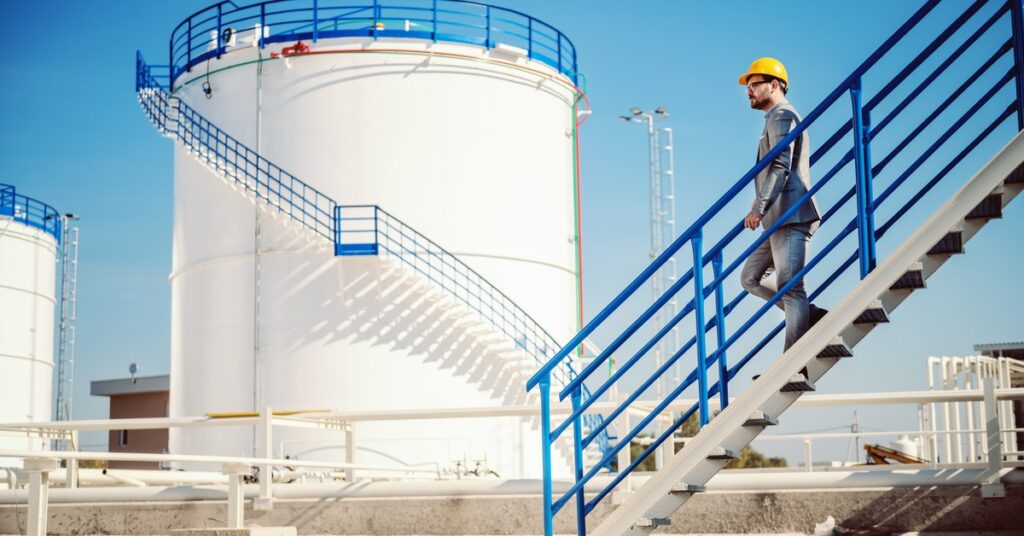
Ceramic-Modified Linings
Ceramic coating technologies incorporate ceramic particles into linings to dramatically improve resistance to abrasion and high temperatures. These linings are particularly beneficial for industries such as mining, power generation, and cement production, where equipment experiences continuous friction and heat. Recent innovations have made these linings lighter and easier to apply without compromising performance.
Graphene-Enhanced Tank Linings
Graphene, hailed as one of the most revolutionary materials of the 21st century, has unmatched strength, impermeability, and thermal conductivity. When integrated into tank linings, graphene significantly enhances durability by reducing wear, tearing, and degradation over time.
Its exceptionally low permeability for gases and liquids ensures superior containment, while its high thermal conductivity adds stability in extreme temperatures. Industries with exacting standards benefit from graphene’s ultra-thin and strong structure. These industries include pharmaceutical manufacturing, high-purity chemical storage, and gas and oil refining.
Additionally, graphene linings can reduce maintenance intervals, saving both time and operational costs.
Self-Healing Coatings
Self-healing linings are an innovative technology that incorporates embedded microcapsules or specialized polymers that can autonomously repair minor damage when triggered by external factors like moisture or heat.
This technology drastically reduces the need for frequent maintenance and enhances the longevity of tank linings by preventing minor damage from escalating into major issues. These coatings are especially valuable in remote or hazardous locations, such as offshore oil rigs or mining operations, where regular inspections and manual repairs can be costly and impractical.
Advanced Polyurea Coatings
Polyurea coatings are setting a new standard in tank lining technology with their rapid curing times, exceptional flexibility, and resistance to extreme conditions. These linings can withstand harsh environments, including exposure to aggressive chemicals, severe temperature fluctuations, and heavy mechanical stress.
The seamless application of polyurea minimizes the risk of leaks or weak points, ensuring reliable performance over time. This resistance makes polyurea coatings a preferred choice for demanding industries such as wastewater treatment, fuel storage, and chemical transport.
Their ability to cure quickly also reduces downtime during application, making them a cost-effective solution for businesses looking to maximize operational efficiency.
Vapor-Phase Corrosion Protection
Vapor-phase inhibitors represent a cutting-edge approach to corrosion prevention. These linings release protective vapors that coat metallic surfaces within enclosed systems, forming a barrier against corrosion. This technology is particularly effective for large industrial tanks or systems with hard-to-reach areas, where traditional coatings may struggle to provide complete coverage.
Bio-Based Linings
With sustainability becoming a key focus across industries, bio-based linings have emerged as an eco-friendly alternative to traditional coatings. Made from renewable resources like plant-based polymers, these linings provide effective corrosion protection while reducing the environmental impact of their production and disposal. They are especially appealing to industries looking to align with green initiatives, such as food and beverage production.
High-Temperature Linings
Tanks used in high-temperature environments, such as oil refining, chemical processing, or power generation, require linings that can withstand extreme heat without degrading. High-temperature linings use advanced materials that resist thermal breakdown, maintaining their structural integrity even at temperatures exceeding 200 degrees Celsius.
These linings not only ensure reliable performance under challenging conditions but also extend the lifespan of tanks and reduce the need for frequent replacements. Their ability to perform consistently in harsh environments makes them invaluable for industries that rely on stable operations in extreme temperature settings.
Dual-Layer Coatings
Dual-layer coatings represent an intelligent combination of materials designed to address multiple challenges simultaneously. For example, one layer may focus on providing exceptional chemical resistance, while the other enhances structural integrity or impact resistance.
This multipurpose approach makes dual-layer coatings ideal for industries where tanks must withstand both corrosive substances and mechanical stress, such as in petrochemical processing and heavy manufacturing.
UV-Curable Linings
UV-curable linings are revolutionizing the application process for tank coatings. These innovative linings cure almost instantly when exposed to UV light, drastically reducing application time and minimizing downtime for businesses. Despite their quick curing process, UV-curable linings offer unmatched hardness, chemical resistance, and durability, making them a reliable choice for industries with tight maintenance schedules.
Their ease of application also means lower labor costs, and their seamless finish ensures long-term protection against leaks and wear. Industries requiring rapid turnarounds, such as food manufacturing or pharmaceutical storage, stand to benefit significantly from this technology.
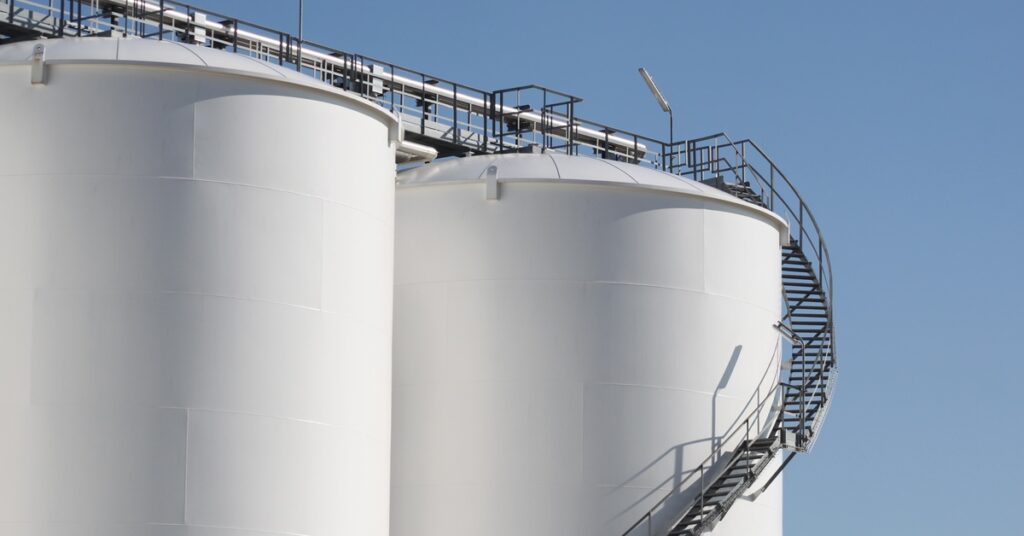
Thermoset Linings
Advances in thermoset polymer technology have led to tank linings with exceptional pressure resistance and chemical compatibility. These linings endure extreme conditions, such as high-pressure environments or exposure to aggressive solvents, without compromising their protective properties.
Highly versatile, thermoset linings are suitable for a wide range of industries, including industrial manufacturing, food processing, and chemical storage. Their robust performance in harsh environments ensures reliable operation and extended tank life, making them a practical choice for businesses seeking long-term solutions.
3D-Printing Technology
3D printing is transforming tank lining design by enabling the creation of custom linings tailored to specific tank shapes and operational requirements. This technology allows for precise application and integration of advanced materials, such as graphene or ceramics, resulting in linings that are highly effective and uniquely suited to demanding environments. By offering customization at an unprecedented level, 3D-printed linings provide a perfect fit for tanks of all sizes and shapes.
Emerging technologies in the world of industrial tank linings are evolving the industry and introducing cutting-edge solutions to tackle age-old challenges. From self-healing coatings to graphene-enhanced linings, these technologies offer unprecedented levels of durability, performance, and efficiency.
By understanding these emerging advancements, you can select the best options to enhance your facilities’ safety, and Flexi-Liner can help. Whether you need cistern liners or something more specific for your industry, you’ll want Flexi-Liner on your side!